Design & Engineering
Precision Manufacturing
Safety Standards
Space Optimization
Quality Assurance
Customizable Options
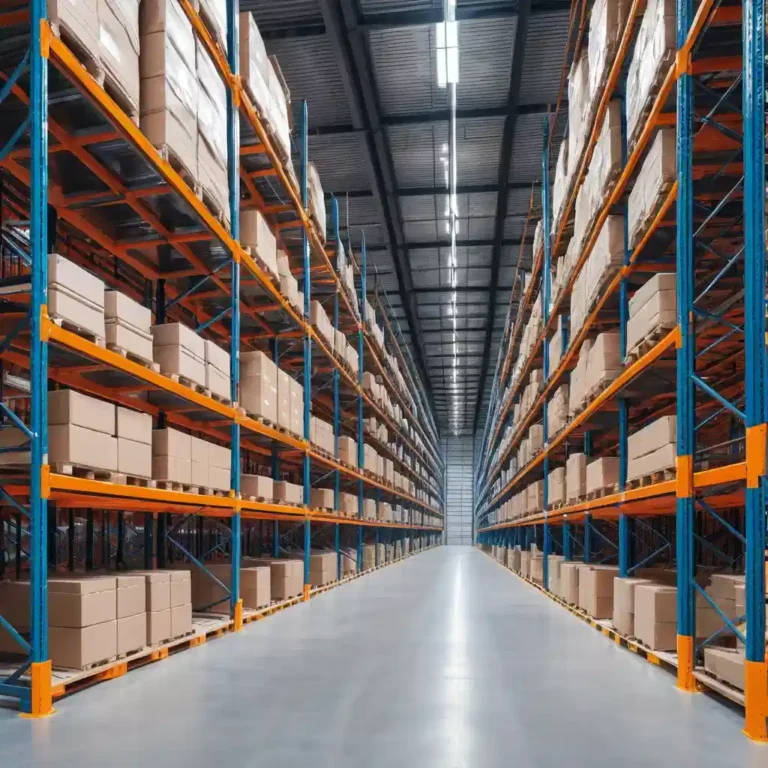
Conventional Pallet Racking
Conventional pallet racking is the most commonly used type of warehouse storage system, designed to store palletized goods in a way that maximizes accessibility and organization. It features rows of horizontal beams that support pallets, creating levels of storage that can be easily accessed by forklifts. This system is popular in various industries, including retail, logistics, and manufacturing, due to its versatility and ease of use.
Key Advantages
- Direct Access: Enables immediate retrieval of every pallet, streamlining inventory management and minimizing time spent on locating goods.
- Flexibility: Allows easy adjustments to accommodate various pallet sizes and configurations, supporting both single-deep and double-deep layouts.
- Cost-Effectiveness: Offers a budget-friendly solution compared to specialized racking systems, with lower installation and maintenance costs.
- Scalability: Features a modular design, making it simple to expand or reconfigure as storage needs grow, ideal for businesses with dynamic inventory requirements.
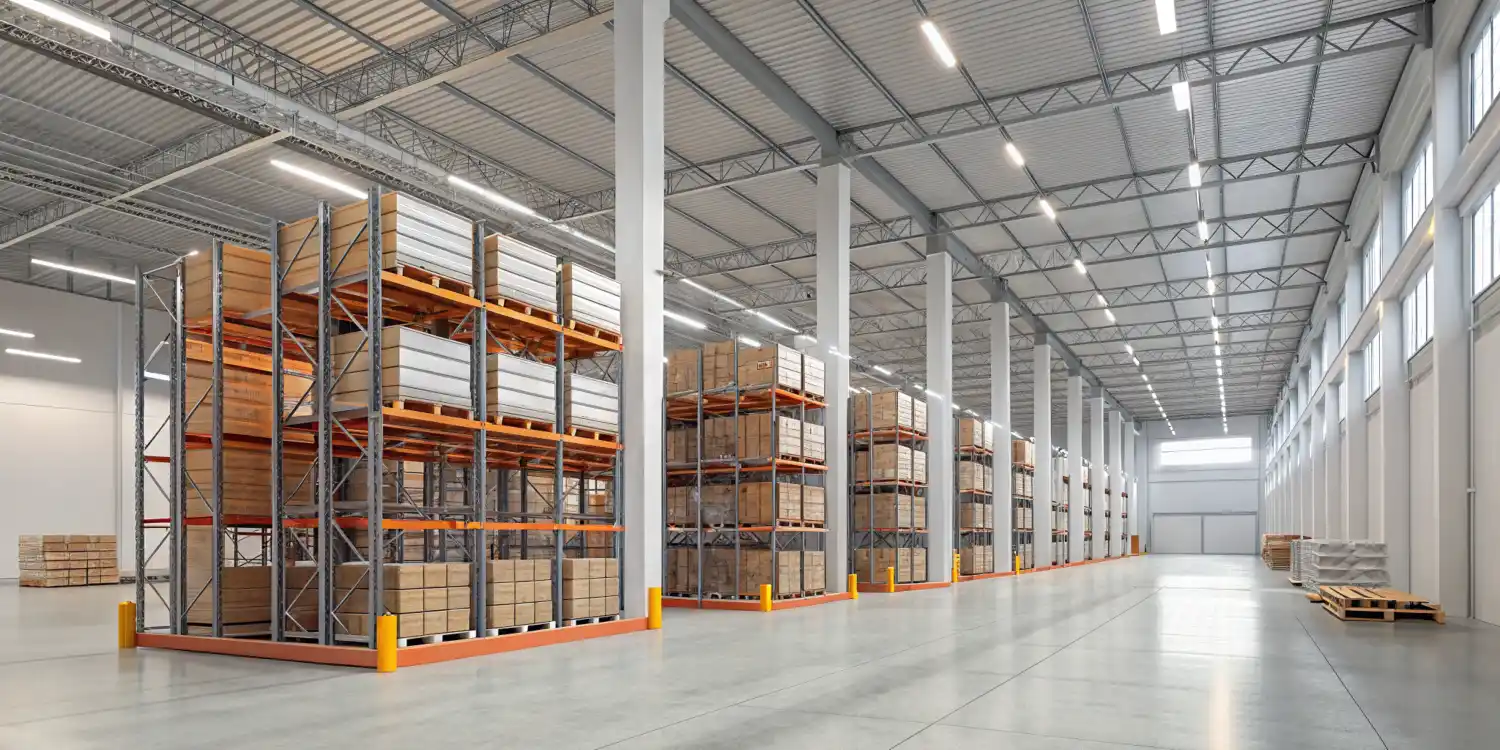